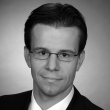
Development engineer, Airbus Defense and Space
Andreas Winkler studied Aerospace at the TU Muenchen from 2000 to 2005 and finished his Diploma in 2005 the North Carolina State University. From 2006 to 2010, he was a Research Associate at the Chair of Aerodynamics at the TU Muenchen, giving a dissertation on the topic "A automated process for the aerodynamic shape development", in 2011. Since 2010 he is Development engineer in the department Aerodynamics & Methods at Airbus Defense and Space.
Speeches
Aerodynamic optimizations carried out at Airbus Defence and Space uses different strategies based on the nature of the problem under investigation and the tools and simulation methods used. For instance, modeFRONTIER implementation of the genetic algorithm is the first choice for problems in which the simulation time is small and the amount of input variable limited. On the other hand, when the analysis time increases to the order of several hours if not days, a gradient based algorithm could be preferred. In fact, optimizations were already carried out in the past at Airbus D&S with the NLPQLP (gradient based) algorithm. In this case, sensitivities were provided to modeFRONTIER by the fluid dynamic solver TAU (developed by the DLR), which has the ability to calculate the input derivatives via the adjoint methodology, therefore limiting the overall optimization time, especially when the amount of variables increases drastically.
There can be other cases in which the use of the adjoint methodology is not the preferred choice, due to some limitations of the code, which is still under development. In such cases, like the example presented here, the optimization algorithm is usually a well known and trusted solution, like the Nelder-Mead (simplex) methodology, which is a very good compromise of speed and robustness.
In the example presented, a real industrial case with all the time and accuracy constraints that this implies, the attention is focused on the tools used to carry out the optimization and their interfaces with the optimization software. Thereby the most challenges arise from the nature of the used analysis method (viscous CFD simulations), whose most salient feature in the context of optimization is the very long computation time which is in the order of several hours. As a consequence it is for example not acceptable in terms of time efficiency to simulate unfeasible designs. Due to the strict constraints coming from other disciplines, the presented optimization problem is populated by a large number of unfeasible/invalid designs, whose handling by the optimization algorithm may affect the final result.