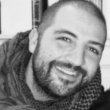
Research fellow, Politecnico di Bari
Antonio Piccininni was born in Bari, Italy, on 23 November 1982. He received the Master’s Degree in Mechanical Engineering from the Politecnico di Bari (Bari, Italy) in 2012 discussing the thesis “Numerical Investigation of the shifting dynamics of a continuously variable transmission” (academic course: Vehicle Design). In 2012, he joined the Department of Mechanical Engineering, Mathematics and Management (DMMM), Politecnico di Bari, as a winner of a trainee grant in the framework of the PON project “SMATI (Sviluppo Materiali Avanzati e Tecnologie Innovative per turbomacchine per impiego in condizioni estreme)”.
He is currently working at the Politecnico di Bari as research fellow, involved in research activities mainly focused on Finite Element simulations (strain distribution in sheet forming processes and analysis of residual stresses in casting processes) and experimental activities about warm hydroforming, warm deep drawing, residual stress measurements and mechanical/technological characterization of metals at elevated temperatures (light alloys and stainless steel).
He is author of a paper about the numerical investigation for the production of an aluminium bipolar plate via warm hydroforming published on the International Journal of Advanced Manufacturing technology; in addition, he is co-author of papers presented at international conferences about sheet metal forming (Numiform 2013 Shenyang, China; ICC International CAE Conference as speaker Pacengo – Lazise, Italy; MetalFORMING 2014 Palermo, Italy) and creep behavior of stainless steel (ECCC Creep & Fracture Conference 2014 Rome, Italy).
Speeches
During the last decade, lower fuel consumption and more limited polluting emissions are the main source of concern for the normative framework. In order to reach such objectives, improvements in terms of vehicle lightweighting must be pursued: reduction of the engine size and structural mass reduction are the most attractive solutions.
As concerns the latter solution, the wider use of light alloys (magnesium, aluminium and titanium) reveals to be an attractive solution. Due to its lightweight and high specific strength, Magnesium (Mg) alloys are widely used by aerospace and automobile industries (production of structural components) and by computer, communication and customer electronic industries (production of covers and thin-walled parts for any kind of devices, like laptop, cell phone, cameras, CD and DVD players).
The most limiting drawback when using Mg alloys is the poor formability exhibited at room temperature due to its Hexagonal Closed-Packed (HCP) crystal structure, in which only the basal plane can move at room temperature. For this reason, thermal activation of further deformation mechanisms becomes necessary to improve ductility and formability. The present work is focused on the investigation of the Deep Drawing process in warm conditions of circular components, aimed at evaluating both the working conditions and the enhancements of the process limits using metamodels.
Experimental tests were carried out using an experimental equipment specifically designed and assembled on a200 kN Standard Tensile Test machine INSTRON 4480: the initial Mg alloy blank was positioned between the die and the blankholder and both of the two were heated by means of electrical cartridge. In order to
enhance formability, the punch was kept at room temperature adopting a cooling system so that a temperature gradient (able to counterbalance the stress gradient originated during the drawing process) could be obtained within the radial direction of the blank.
A first experimental campaign was carried out with the aim of investigating the effect of the most important process parameters affecting the forming of sound cups: the blank holder pressure, the temperature of the Blank holder and the punch speed. The output variable “Progress” (punch stroke/max punch stroke) was fitted adopting two different Response Surface (RS) algorithms, respectively a second order polynomial SVD and a Radial Basis Function (RBF); the determined surfaces were the starting point for the subsequent initial optimization.
Basing on the virtual designs coming from the previous optimization, a second experimental activity was carried out aimed at investigating the process limits according to temperature and punch speed: in particular, in this second experimental campaign blanks having different diameters were used and the maximum drawing ratio (Limit Drawing Ratio) was evaluated for different temperature and punch speed levels. In this second case, even considering a separate approach based on two different RS algorithms, optimization results
were similar. These last results were used as a validation for those coming from the initial optimization, stating in this way which of the two initial RS was the most reliable in evaluating the process window.