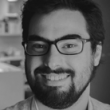
Visiting Research Scholar, MIT
Giuliano Vernengo is Visiting Research Scholar at MIT Sea Grant College Program Design Lab, under the supervision of Prof. Stefano Brizzolara. His research is actually focused on the development of a non-linear 3D vortex lattice method able to solve the steady hydrodynamic problem of stepped planning craft in calm water. The method is able to accomplish both the performance analysis of given hull and the design of innovative hull forms with and without transversal steps. He is also involved in the development of an advanced numerical Smoothed Particle Hydrodynamic (SPH) solver, which exploit GPU computational techniques, for the solution of the 2D wedge impact problem with variable-shape wedges.
His background in numerical methods for ship design covers two major topics: the application of parametric description of complex hull shapes aimed at the hydrodynamic shape optimization with respect to both calm water resistance, analyzed by means of BEM methods, and seakeeping, studied via strip theory based methods; the development of Ship Synthesis Model (SSM) for the preliminary assessment of a fleet of ships for a given trade, with specific attention on the effect of the added resistance on the overall economic performance of the trade itself.
For the University of Genoa, he is still carrying on the preliminary hydrodynamic design of a “zero-emission” ferry for short coastal cruises, with an innovative hull form and hybrid electric propulsion.
Education:
Ph.D. in Numerical Naval Architecture, University of Genoa, Italy, 2012. Dissertation on “Parametric Hydrodynamic Optimization of Ship Hull Forms based on CFD Techniques: Theory and Application”.
Speeches
Authors: Giuliano Vernengo & Stefano Brizzolara | MIT Innovative Ship Design Lab (i-Ship), Massachusetts Institute of Technology, Cambridge, MA, USA
In order to create a robust hydrodynamic shape optimization process, three main topics have to be integrated: an effective geometric description of the hull surfaces; robust numerical methods for the prediction of hydrodynamic performance and a smart optimization procedure able to drive the whole optimization process towards the best hull form solution.
Recent fully parametric modeling tools have been specifically adapted for ship hull forms. These software tools permit to setup a relational geometry structure to mathematically define complex 3D surfaces as a function of a set of scalar variables controlling the geometric properties of surface. Various parametric surface models can be conceived and generated using these tools, but only few of them can effectively integrated into automatic computer driven procedures and efficiently used for parametric ship hull form optimization.
The MIT Innovative Ship Design Lab (MIT i-Ship) is actively participating to technological advancements in this new field, concentrating by tradition on numerical technologies for hydrodynamic solvers, but also on the development of robust and reliable parametric hull models of different type of ships (both traditional and unconventional), as well as on the definition of formal design by optimization frameworks which can accelerate the selection of the best hull shape.
In fact, another important aspect of ship hull form optimization is the numerical estimation of the hydrodynamic performance: there exist several possibilities ranging from low to high fidelity methods. The computational time, of course, dramatically changes from one another, as well as the level of accuracy of the results. Several studies has been dedicated to assessing the robustness and the efficiency of each of these methods. For instance starting from the lowest to the highest numerical hydrodynamic methods the designer has the possibility to choose from lower-fidelity statistical or empirical prediction tools, which do not account for the real shape of the hull but only for some its shape global parameters; the medium-fidelity numerical hydrodynamic solvers, such as steady and unsteady boundary elements methods (BEM) to solve the wave resistance/seakeeping problem, where the actual 3D hull shape is considered; up to the higher-fidelity solvers, such as time domain, multi-phases, turbulent viscous RANSE solvers.
Currently the best trade-off to perform most of the hydrodynamic shape optimization problems is to use medium-fidelity solution methods, where MIT-iShip has developed specific BEM solvers that consider most of the non-linearities of the hydrodynamic problem that are important for an accurate prediction of the hull hydrodynamics in calm water and in waves.
Intelligent optimization algorithms together with HPC clusters can create new perspectives to speed up the overall optimization task, opening the way to the integration of higher-fidelity solvers into hybrid multi-fidelity optimization procedures or to more complex multi-objective optimization of ship performance, as those including resistance, seakeeping and propulsion performance.
After giving a general picture on this new concept of ship design by numerical optimization, the main goal of the proposed work is to show how the choice of the optimization algorithm, or more generally of the optimization approach, using the modeFrontier optimization environment, should affect both the overall performance of the process as well as the accuracy of its results.
The same hydrodynamic optimization problem, e.g. resistance and seakeeping optimization of a displacement vessel, is hence tackled by means of different approaches. First, a multi-objective genetic algorithm is used to drive the optimization test and a sensitivity study on its setting parameters is performed and discussed. The second test case exploit the use of the attractive Response Surface Method (RSM), coupled with a population based algorithm, to gain the speed up of the whole computational time.