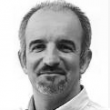
Professor, University of Technologie of Troyes
Prof. Pascal Lafon has obtained his PhD degree in 1994 from Paul Sabatier University in Toulouse, on the subject of "Optimization of Mechanical System in mixed variables". Pascal Lafon has been associated professor from 1994 to 2009 and full professor since 2009. He is currently the head of the Laboratory of Mechanical Systems and Concurrent Engineering.
He has written or co-written more than 80 publications in paper and conference and he is interest in the following areas:
- Product life cycle management
- Optimization of mechanical system and of forming/stamping process
- Reliable optimization with uncertainties
- Multi objective optimization and stochastic algorithm
- Response surface modelling, Proper Orthogonal Decomposition
Speeches
Taking into account variation of noise factors is a very critical issue in order to enhance the robustness of the sheet metal stamping process in the product design process. The stochastic variability of the uncontrollable process variables results in the scattering on the produced part which can lead to rejected parts.
Due to the fact that the inherent sources of variation in the sheet metal stamping process comes from part-to-part, within batch and batch-to-batch variation. Therefore, the control of the variability influencing on the performance of the product is an essential demand of automotive or aeronautic industries. Also, it is very necessary to have a numerically dedicated tool which predicts the process variability with a good confidence. In this paper, prediction of the impact of the variation of several parameters on the finally stamped open-channel part by numerical simulation will be carried out in the detailed design phase.
As a result, springback defect is described by geometrical parameters and tolerance zone. These descriptions are used in different context: the parameter description is used in process optimization. In addition, to evaluate the degree of reliability of Finite Element Analysis (FEA) software, namely ABAQUS™ software, sensitivity analysis of the blank thickness variation in U-shaped stamping process is employed. This approach provides a procedure to take into consideration the effect of the stamping process variations on the variability of the stamped part by using the numerical simulation. Virtual stamping process is modeled and simulated in the ABAQUS™, and then calculation of descriptions of the stamped part’s variations is carried out in the Matlab software.
Subsequently, the ABAQUS™ and MATLAB™ node are coupled in the workflow of modeFRONTIER™ to optimize the stamping process. This proposed design tool contributes to reduction of tooling design time as well as elimination of expensive physical experiments in the very previous step on the product lifecycle.