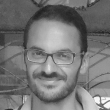
Senior Research Fellow, The University of Warwick
Dr. Pasquale Franciosa is Senior Research Fellow at University of Warwick (UK) - Warwick Manufacturing Group (WMG). His has extensive expertise in modelling and simulations of compliant/deformable assemblies, tooling and multi-disciplinary/multi-objective optimization. He earned his PhD (Mechanical Engineering System at the University of Naples Federico II, Italy) focusing on modelling and simulation of non-ideal assembly process specifically: (i) dimensional and geometrical variations impacting key performance indicators (KPIs), (ii) rigid and compliant/deformable parts (power-train or body in white assembly systems), and (iii) non-ideal parts going beyond nominal CAD products embedding manufacturing errors. He has contributed on several academic and industrial projects involving (i) dimensional management control and innovative tools to predict stack-up of variations propagating in multi-stage systems, (ii)CAD and FEA modelling, and (iii) multi-physics applications for product performance assessment. His current research focuses on the development of systematic methodology and toolsets for modelling, analysis and in-process quality control of a Reconfigurable Assembly System integrated within multi-station assembly system with deformable parts. He is the leader of the process design and optimisation work-package for the FP7 RLW Navigator project on a novel joining process for automotive assembly (www.rlwnavigator.eu). He is author and co-author of about 40 papers, published on international peer-reviewed journals and conferences. As part of his research he is regular referee of the (i) International Journal of Advanced Manufacturing Technology (IJAMT), (ii) International Journal Interactive Design and Manufacturing (IJDeM), and (iii) Medical Engineering and Physics (MEP).
Speeches
Geometric or dimensional variation is one of the most important quality and productivity factor in fabrication and assembly processes. It is even more critical with introduction of new materials, need for multi-material assemblies and as a consequence requirement for hybrid joining processes.
For new and emerging applications such as remote laser welding (RLW) variation is recognised as one of the most crucial barriers that prevents delivery of high quality product. Indeed the joint quality is directly related to the part-to-part gap which is imputed to dimensional and geometric variation of stamped sheet-metal parts.
Over the years, a number of studies have investigated product variation of compliant parts. However, there is a lack of “non-ideal” compliant part models for accurate assembly process simulations. Both research and industry practices have underscore the need for fast and reliable simulation approaches that can quickly identify final assembly variations, isolate product failure patterns and suggest corrective actions to deliver high product quality. Simulation capability at the DLM (Digital Lifecycle Management) Research Group spans from product/process design to process control and adjustment for dimensional management in multi-station assembly process with compliant non-ideal parts (sheet-metal part/sub-assembly).
This talk presents methods and tools for modelling and simulation of assembly processes with non-ideal compliant parts joined using Remote Laser Welding (RLW) processes. We address: (i) fixture optimiser for “non-ideal” compliant parts; (ii) RLW joining process parameters optimiser; (iii) design synthesis of (i) and (ii); and, (iv) interactive design synthesis framework for additional external design tasks (i.e., joints location layout). This talk will cover in particular (i) and (ii). The developed methods and simulation tools have been successfully tested and validated using industrial case study of automotive door assembly with RLW joining process. The following benefits and impact have been achieved when compared to state-of-the-art and state-of-the-practice in industry: (1) 25% reduction in engineering changes necessary in today’s industrial practice. At present, these changes in industry practice are done after the production fixtures are built which significantly increases both cost and time necessary to have production ready fixtures. (2) 20% increase of product quality as compared to current industrial practice. This comparison was done based on the door quality after all the necessary engineering changes were done for state-of-the-practice approach. (3) the developed approach and tool has capability to provide: (i) models linking explicitly the interrelations between Key Product Characteristics (KPCs) and Key Control Characteristics (KCCs); (ii) fixture optimization, not only for a single non-ideal part; but also for a batch of parts. This allows obtaining optimized fixture which is design for a volume of production (“non-ideal”) parts; rather than a single “ideal” or “synthetic” part as is current industry practice. (iii) interactive/collaborative framework between process designers and product design engineers. The approach can provide graphical information showing part deformation for given joint stitch layout; and given optimized clamp layout.
Currently, the tool does not optimize stitch layout; however, it can be used for graphically presenting part-to-part gap for given stitch at the optimized clamp layout. This can help product and process design engineers to understand the consequences of changing clamp layout (for e.g. by adding clamp(s) which might be expensive) or by changing location of a stitch or changing type of stitch (linear vs. circular or staple stitch). The developed tools have been implemented in MatLAB and integrated in modeFrontier.