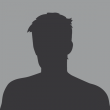
Design and Development Engineer, HYDAC Cooling GmbH
Thomas Wolfanger received his degree as Mechanical Engineer from University of Kaiserslautern in 1993. From 1999 to 2009 he worked as a reseach scientist at TLT Turbo GmbH, Zweibrücken, Germany in the field of wind tunnel and fan design and optimisation. In 2001 he earned his PhD in Mechanical Engineering from University of Kaiserslautern on the usage of nonlinear turbulence models for atmospheric flow over complex terrain. Since 2009 till he has been working as a Design and Development Manager at Hydac Cooling GmbH, Sulzbach, Germay in the field of cooler develompent and application research
Speeches
OPTIMHEX Project (Virtual platform for design and optimization of compact Heat Exchangers) is funded by Eurostars Programme powered by EUREKA and European Community. The project consortium is formed by: HYDAC AG, Swiss multi-national company that produces compact plate-fin Heat Exchangers for industrial and mobile sectors; SUPSI – ICIMSI, the Swiss Institute for computer integrated manufacturing belonging to the Department of Innovative Technologies of SUPSI University; UNIVERSITY OF TRIESTE, Department of Architecture and Engineering; ESTECO. The main purpose of the project is the study and development of an innovative methodology for Heat Exchangers (HE) design, based on the definition of a software package managed by modeFRONTIER, a multi-objective optimization software produced by ESTECO, able to create HE virtual models by targeting HE performance, optimal use of material, HE minimal weight and optimal manufacturability.
This means that the HE design procedures at HYDAC will be driven by tools able to target products optimized in terms of production processes, material used, expected performances, and efficiency. The complexity of heat removal/transfer is linked to the interaction of several factors and variables. Heat exchange depends on the characteristics of the fluids used, on the material, geometry and dimensions of the heat exchanger (HE), on the geometry and dimension of the heat transfer surface, on the working conditions such as temperature, pressure and flow rate, on the fluid flow characteristics, on the climatic and operative conditions.
The challenge of this project is to combine scientific and engineering approaches to tackle the objective of enlarging and deepening the industrial knowledge leading to high technology products and processes. The proposed methodology consists in the definition of a workflow for the automatic CFD simulation of a parametric model of a periodic HE cellular element, the definition of a Response Surface covering all the possible range of parameters’ combination, the definition of a analytical “bridge” models to extend the behavior of the liquid and air HE cellular elements to a real scale HE, and an optimization process to obtain the optimal HE design for any proposed application and requirements.
In this paper the main aspects covering the background of the project, the proposed methodology and the expected benefits will be introduced. In addition, validation of the CFD models with experimental data available in the literature will be illustrated, as well as a simple optimization example using a well-known “bridge” method from literature.